Automotive Gas Divider
The Environics® Series 4040 Automotive Gas Divider is an advanced instrument for the dynamic calibration of automotive or mobile source emissions analyzers. This system stands out from competitors in its ability to generate infinitely varied concentrations within the operating range of the instrument, protecting your investment and giving you the needed flexibility should standards change.
Units can now be ordered or retrofit to run on a 24V power source so you can use your unit anywhere.
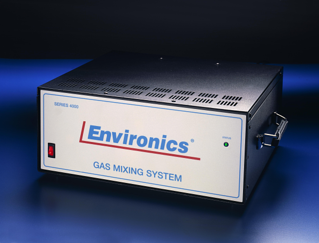
The Series 4040 automatically performs standard ten-step dilutions of all calibration gases in accordance with U.S. Environmental Protection Agency protocols. The system may also be used to generate calibration standards in user specified concentrations (%, ppm or ppb) by dynamic dilution of higher concentration source cylinders.
This system stands out from competitors in its ability to generate infinitely varied concentrations within the operating range of the instrument, protecting your investment and giving you the needed flexibility should standards change.
The mixes are highly repeatable and unlike many dividers, the Environics system is accurate to +/-1% of setpoint.
The Series 4040 consists of a single chassis supporting three thermal mass flow controllers, a serpentine pre-mix zone and a zero dead space final mixing zone. All gas wetted surfaces are electropolished stainless steel, and seals are gas compatible elastomers. The instruments mass flow controllers are factory calibrated using a primary flow standard traceable to the United States National Institute of Standards and Technology (NIST).
The user interface is a Microsoft® Windows application that communicates with the Environics system via a USB (standard) or RS232 serial interface.
Bluetooth enabled devices running Windows software can also control the unit remotely (optional).
Additional options include the ability to remote start, remote stop, and canister filling stop all via a dry contact closure. Optional alarms available and can include visual alarms upon low input cylinder pressure.
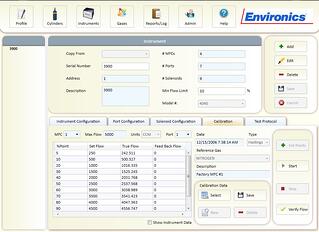
- Automated 10 step divide mode which allows user to specify divide points, dwell time and sequence provides operational flexibility and saves technician time.
- Design which allows the user to go as low as a 1% step (% of cylinder gas concentration) with no loss of accuracy. The user can generate a wider range of standards with each cylinder thus saving on gas costs.
- Outputs permit integration with existing and future automotive emissions test benches.
- Gas mixing on a mass flow basis eliminates complicated pressure controls and inaccuracies due to critical orifice erosion and temperature variations.
- Internally-stored mass flow controller calibration data improves accuracy by as much as a factor of ten and simplifies field recalibration.
- Modular design allows for additional gas circuits to be added.
- User definable cylinder library allows for easy selection of frequently used gas cylinders. Each cylinder may contain an unlimited number of component gases with automatic K-factor calculation.
- Easy to operate software included. How-to videos available.
- DLL Drivers Available
- Concentration Mode Allows user to create a blend by entering target gas concentrations for each source gas cylinder, and the desired total output flow for the mix.
- Divider Mode Allows the user to operate the instrument as an automated ten step gas divider.
- Flow Mode Allows user to specify the flow rate of each gas cylinder.
- Program/Schedule Modes Provides the ability to program the instrument for unattended operation. Programs can be recalled and run in any sequence, at various times/dates.
- Purge Mode (optional) Allows user to flush the gas flow path from a designated input port. User can define the flow rates used and can purge any combination of component MFCs.
- Accuracy
- From 10 to 100% of Full Scale Flow
- Concentration: ± 1.0% setpoint
- Flow: ± 1.0% setpoint
- Repeatability: 0.05%
Performance specifications are valid when all Mass Flow Controllers are operating between 10% and 100% of full scale flow. Mass flow controllers are calibrated using a NIST traceable Primary Flow Standard, using a Reference Temperature of 0°C (32°F) and a Reference Pressure of 760 mm Hg (29.92 in. Hg).
Mechanical
- Inlets
- Dilution: External 1/4" SwagelokTM
- Span(s): External 1/4" SwagelokTM
- Ozone source gas: External 1/4" SwagelokTM
- Outlet: External 1/4" SwagelokTM
- Operating Pressures
- Minimum: 10 psig (0.67 Bar)
- Recommended: 25 psig (1.68 Bar)
- Maximum: 75 psig (5.04 Bar)
- Wetted Surfaces
- Tubing: Electropolished 316L Stainless Steel
- MFC's: Stainless Steel
- Seals: Viton®
- Operating temperature: 32° - 122° F (0° - 50° C)
- Performance temperature: 59° - 95° F (15° - 35° C)
- Weight
- 2 MFC System: 18 lbs.
- 4 MFC System: 23 lbs.
- Dimensions (w x h x d)
- Portable: 17" x 7" x 15"
- (43.18 cm x 17.78 cm x 38.1 cm)
- Rack: 19" x 7" x 15"
- (48.26 cm x 17.78 cm x 38.1 cm)
Electrical
- 100 to 250 VAC, 50/60 Hz; 24V now available.
Electronics
- 12 Bit A/D and D/A Conversion
- USB (standard) or RS232 Serial interface
Software
- Environics Instrument Control Software (supplied on thumbdrive or via download). How-to videos available.
- DLL Drivers Available
PC Requirements
- IBM PC or compatible (486-33 or higher)
- Windows 7/8/10
- 1GB RAM
- 100 MB Hard Disk Space
- USB (standard) or RS-232 Communication port
Viton® and Kalrez® are registered trademarks of Dupont Dow Elastomers
- Additional input ports (up to 8)
- Additional MFC's (up to 8)
- Various Seal Materials including Teflon and Kalrez
- Cleaned for Oxygen Service
- Humidification
- Permeation
- Silicon Coated Gas Path
- Purge Circuit
- Heated Flow Path
- Canister Filling
- Explosive Gas system