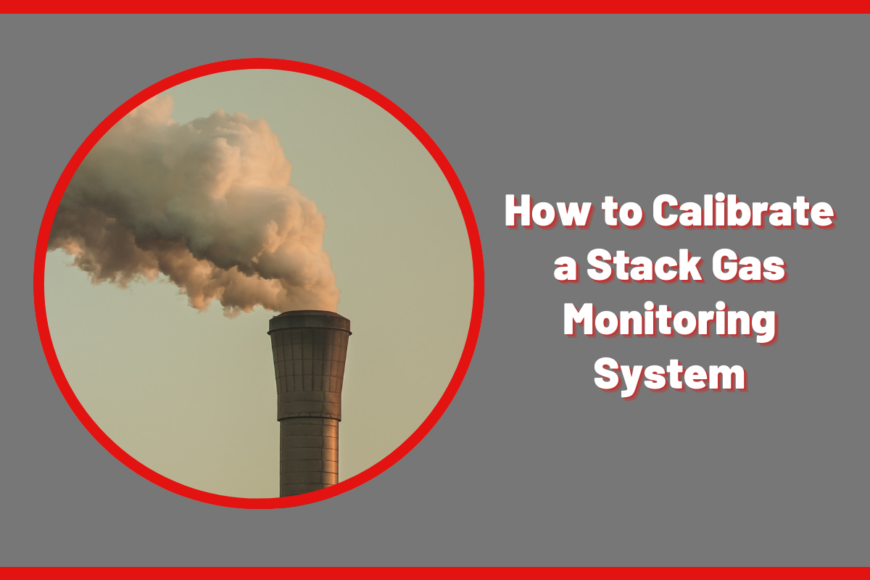
Stack gas monitoring systems are indispensable for measuring emissions from industrial processes, ensuring compliance with environmental regulations and contributing to sustainable industrial practices. Accurate systems calibration is critical for providing reliable emissions data, which forms the foundation of regulatory reporting and environmental protection strategies.
Components of a Stack Gas Monitoring System
A typical stack gas monitoring system consists of several key components, each playing a vital role in capturing and analyzing emissions data:
- Sample Probes: Extract gas samples from the emission source.
- Gas Analyzers: Detect and measure concentrations of pollutants such as sulfur dioxide (SO₂), nitrogen oxides (NOₓ), carbon monoxide (CO), carbon dioxide (CO₂), and oxygen (O₂).
- Calibration Gas Systems: Deliver known concentrations of calibration gases to verify analyzer accuracy.
- Data Acquisition Units (DAUs): Collect, process, and store emissions data for regulatory reporting.
Proper calibration of these components ensures the system’s overall accuracy and reliability.
Importance of Calibration
Calibration is the process of verifying and adjusting the accuracy of gas analyzers to ensure they provide correct readings. This process is essential for several reasons:
- Regulatory Compliance: Many environmental regulations mandate regular calibration to maintain data integrity.
- Data Accuracy: Calibration minimizes measurement errors, providing reliable data for environmental reporting.
- Equipment Performance: Regular calibration helps detect and correct analyzer drift, maintaining consistent performance.
- Operational Efficiency: Accurate data supports better decision-making in emissions control strategies.
Types of Calibration
Calibration can be categorized into several types, each serving a specific purpose in ensuring analyzer accuracy:
1. Zero Calibration:
Establishes a baseline measurement using a zero gas, typically high-purity nitrogen, to ensure the analyzer reads zero when no target gas is present.
2. Span Calibration:
Uses a certified calibration gas with a known concentration of the target pollutant to verify the analyzer’s response and accuracy.
3. Multi-Point Calibration:
Involves using multiple calibration gases at different concentrations to assess the analyzer’s linearity and response across a range of emission levels.
Calibration Procedure
A standardized calibration procedure ensures consistency and accuracy. The general steps include:
1. Preparation:
- Confirm the system is operational and stable.
- Select certified calibration gases with traceable standards.
- Ensure environmental conditions are stable to prevent external factors from affecting the calibration.
2. Zero Check:
- Introduce zero gas to the analyzer.
- Verify that the reading is at or near zero; adjust if necessary.
3. Span Check:
- Apply span gas with a known concentration.
- Compare the analyzer’s reading to the known value.
- If discrepancies are found, adjust the analyzer settings to correct the deviation.
4. Adjustments:
- Fine-tune the analyzer to align with the calibration standards.
- Repeat zero and span checks after adjustments to confirm accuracy.
5. Documentation:
- Record all calibration activities, including gas concentrations, analyzer readings, adjustments made, and environmental conditions.
- Maintain detailed logs for regulatory audits and compliance verification.
Best Practices for Calibration
To ensure optimal calibration results, adhere to the following best practices:
- Regular Calibration: Follow manufacturer recommendations and regulatory requirements for calibration frequency.
- Use High-Purity Gases: Utilize certified calibration gases with high purity and traceable standards.
- Stable Conditions: Conduct calibration in stable environmental conditions to reduce variability.
- Routine Maintenance: Regularly inspect and maintain system components to prevent calibration errors.
- Training: Ensure personnel conducting calibrations are properly trained and knowledgeable about the equipment and procedures.
Interested in Stack Gas Monitoring Solutions?
Accurate calibration of stack gas monitoring systems is not just a regulatory requirement; it is a cornerstone of environmental stewardship and sustainable industrial operations. By ensuring precise emissions data, industries can make informed decisions, optimize emissions control strategies, and demonstrate compliance with environmental standards.
Environics plays a pivotal role in supporting industries with advanced gas dilution and calibration systems. Our solutions are designed to enhance the precision and efficiency of stack gas monitoring system calibrations:
- Advanced Gas Dilution Systems: Provide accurate and customizable gas mixtures for multi-point calibrations.
- Regulatory Compliance Support: Ensure calibration processes meet global standards, including EPA, EU, and ISO requirements.
- Automated Solutions: Reduce manual intervention, minimizing human error and improving data consistency.
- Technical Expertise: Offer comprehensive support and training to help industries implement best calibration practices.
Our cutting-edge calibration solutions empower industries to achieve these goals, fostering a cleaner, more sustainable future.