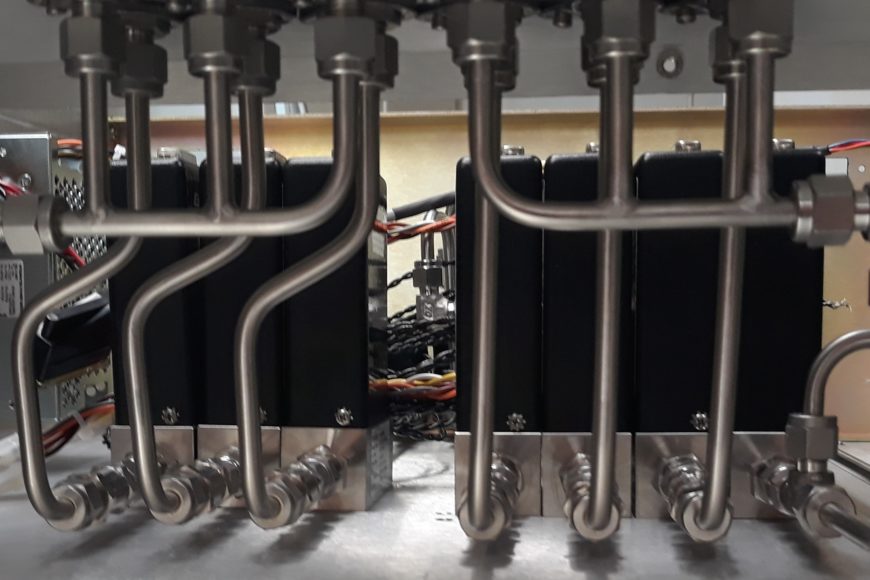
Ultra-low concentration gas mixing is a sophisticated process crucial for areas requiring precise control over mixed gases, such as the semiconductor and food industries. This gas mixing technology is also vital for applications where the accurate generation of specific gas concentrations is imperative, including sensor calibration, atmospheric monitoring, and specialty gas production. By learning about the mechanics of ultra-low concentration gas mixing, we can appreciate its role in achieving high precision and reliability in gas applications.
Understanding Ultra-Low Concentration Gas Mixing
Achieving ultra-low gas concentrations often involves specialized equipment and techniques to ensure accuracy and prevent contamination. Three of the most commonly used methods include:
SilcoNert Coating
SilcoNert coating is applied to gas paths to prevent loss due to adhesion. This coating reduces the absorption of gases on the internal surfaces of the mixing equipment, thereby maintaining the integrity of ultra-low concentration gas mixtures.
Ultra-High Purity Systems
Ultra-high purity systems, particularly those with welded designs, are essential for preventing elastomer seal permeation into and out of the gas path. These systems ensure that no contaminants compromise the gas mixture and no gas is lost, which is critical for maintaining ultra-low concentrations.
Double Dilution Process
The double dilution process is another technique employed to achieve even lower gas concentrations. It involves two sequential dilution steps:
1. Initial Dilution: The concentrated gas is first diluted with a balance gas to a lower concentration, often at a fixed ratio like 1000:1.
2. Serial Dilution: A portion of the initially diluted gas is further diluted in a second step to achieve the desired ultra-low concentration. This method allows fine-tuning but has a trade-off in accuracy, +/-1% per dilution stage.
Permeation Systems
While the primary focus is on cylinder-based methods, permeation systems are an alternative worth mentioning for their cost-effectiveness and specific applications.
Components and Process
A permeation system includes several critical components: a permeation oven, mass flow controllers (MFCs), temperature controllers, and disposable or LF (refillable) permeation tubes containing the liquid phase of the target compound.
– Permeation Oven: The permeation tubes are placed inside the heated oven, facilitating the vaporization of the liquid compound. The temperature can be adjustable to accommodate multiple compounds.
– Vapor Permeation: The vapor permeates through the tube’s polymeric membrane at a controlled rate with a carrier gas and is then used directly or diluted with a balance gas regulated by MFCs to achieve the desired concentration.
Advantages of Permeation Systems
– On-Demand Gas Generation: This ensures gas freshness and avoids adsorption issues common with pre-mixed cylinders.
– Stable and Predictable Rates: Permeation systems can achieve highly stable and predictable rates down to parts-per-billion (ppb) levels.
– Cost-Effective: Particularly for low concentrations, disposable permeation tubes are more cost-effective than pre-mixed cylinders.
Applications and Importance
The ability to generate highly accurate gas concentrations is essential in various fields. For example:
– Sensor Calibration: Ensuring the accuracy and reliability of sensors used for detecting pollutants or other critical compounds.
– Atmospheric Monitoring: Crucial for studying trace gases that influence climate change.
– Semiconductor Manufacturing: Necessary for producing high-quality electronic components.
Undertaking Ultra-Low Concentration Gas Mixing Requires Robust Equipment
Ultra-low concentration gas mixing, achieved through methods such as SilcoNert coating, ultra-high purity systems, and double dilution, is essential for numerous scientific and industrial applications. Permeation systems provide a cost-effective alternative for specific needs. At Environics, we pride ourselves on offering advanced gas mixing systems tailored to our clients’ specific requirements. Whether you need a device for calibrating gases below 1%, like our Series 6100 NO/03, or a system that allows higher level starting gases like our Series S4000 Gas Mixing System, we have the perfect solution. For more information, speak with our experts or visit our blog page for topics related to gas mixing, blending, and dilution. Enhance your work with our ultra-low concentration gas mixing equipment; the perfect device is waiting for you on our website.