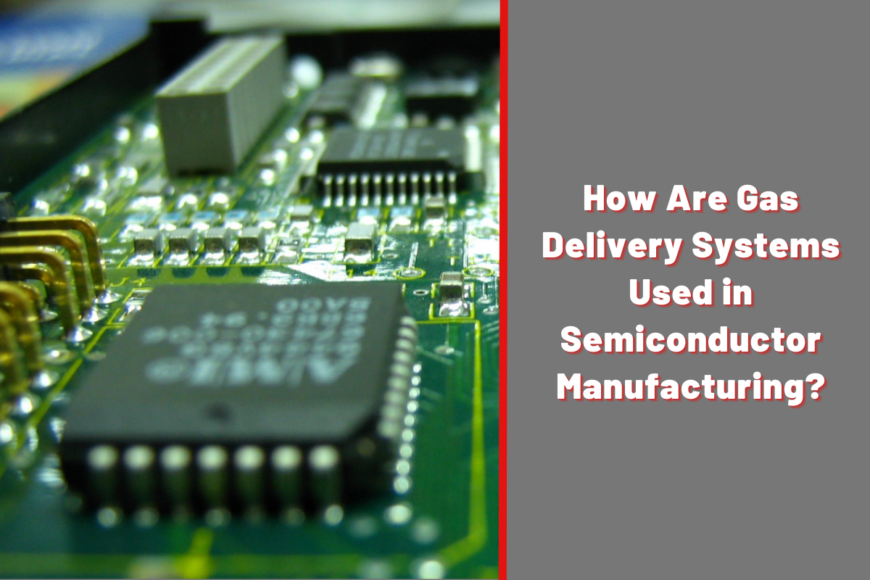
Gas delivery systems are fundamental to the semiconductor manufacturing process, where precision, safety, and efficiency are paramount. These systems enable meticulous control over the flow and composition of gases, which are crucial for processes like etching, doping, and deposition. Let’s dig into the role of gas delivery systems in semiconductor fabrication.
Functions in Semiconductor Processes
Gas delivery systems perform several critical functions in semiconductor manufacturing, each requiring exceptional precision to maintain product quality and process efficiency:
1. Deposition
- Chemical Vapor Deposition (CVD): Involves the chemical reaction of gaseous precursors to form thin films on semiconductor wafers. Precise gas mixtures are essential to control film composition, thickness, and uniformity.
- Physical Vapor Deposition (PVD): Utilizes physical processes like sputtering to deposit materials. Controlled gas flow ensures the stability of plasma and uniform coating.
2. Etching
- Reactive Ion Etching (RIE): Uses reactive gases such as sulfur hexafluoride (SF₆) and chlorine (Cl₂) to selectively remove material from the wafer surface, enabling intricate pattern transfers with nanoscale precision.
3. Doping
- Introduces impurities into semiconductor materials to modify electrical properties. Gases like phosphine (PH₃) and arsine (AsH₃) are used to achieve controlled doping levels, critical for device performance.
4. Purging and Cleaning
- Inert gases such as nitrogen (N₂) and argon (Ar) are employed to purge process chambers, maintain contamination-free environments, and clean equipment between production cycles.
Components of Gas Delivery Systems
A sophisticated gas delivery system comprises various components, each designed to maintain precise control over gas flow, composition, and purity:
- Gas Cabinets: Secure enclosures housing gas cylinders, equipped with safety interlocks and monitoring systems.
- Mass Flow Controllers (MFCs): Regulate the flow rate of gases with high accuracy, essential for process consistency.
- Valves and Regulators: Control the pressure and direction of gas flow, ensuring stable delivery conditions.
- Purifiers: Remove contaminants to achieve ultra-high purity (UHP) levels required in semiconductor processes.
- Manifolds and Piping: Distribute gases efficiently to various process tools while maintaining integrity and cleanliness.
Precision and Safety Considerations
Semiconductor manufacturing demands extremely high levels of gas purity to prevent defects in microelectronic devices. Even trace contaminants can compromise yield and performance. UHP standards are maintained through specialized materials, cleanroom environments, and advanced purification technologies.
Handling reactive and hazardous gases necessitates robust safety protocols:
- Leak Detection Systems: Continuous monitoring for gas leaks to prevent accidents.
- Emergency Shut-Off Valves (ESVs): Automatically isolate gas supplies in the event of a detected hazard.
- Pressure Relief Devices: Prevent over-pressurization, reducing the risk of system failures.
- Redundant Monitoring: Ensures critical parameters like pressure, flow, and composition are consistently within safe limits.
Environics’ Contributions to Semiconductor Manufacturing
Environics plays a pivotal role in enhancing the efficiency and safety of gas delivery systems for the semiconductor industry. Our advanced solutions include:
- Ultra-High Purity Gas Mixing and Dilution Systems: Designed for precise control of gas mixtures, ensuring consistency and repeatability in critical processes.
- Customizable Gas Delivery Solutions: Tailored to meet the specific requirements of semiconductor fabs, from R&D environments to high-volume manufacturing.
- Automated Control Systems: Enhance process efficiency by reducing manual intervention, minimizing the risk of human error.
- Expert Support and Consultation: Providing technical expertise to optimize gas handling systems for performance, safety, and compliance.
Emerging Trends in Gas Delivery Systems
The semiconductor industry is rapidly evolving, driving new demands on gas delivery technologies:
- Advanced Materials for Next-Generation Chips: The development of new semiconductor materials, such as compound semiconductors and 2D materials, requires innovative gas delivery solutions.
- Miniaturization and Precision: As device features shrink to atomic scales, the demand for ultra-precise gas flow control becomes increasingly critical.
- Sustainable Gas Management Practices: Growing emphasis on environmental sustainability has led to the adoption of gas recycling technologies and energy-efficient system designs.
Looking for Semiconductor Manufacturing Gas Solutions?
Gas delivery systems are the backbone of semiconductor manufacturing, enabling precise, safe, and efficient handling of process gases. Their role extends beyond basic gas supply to encompass advanced control, safety, and environmental stewardship. Environics’ cutting-edge gas mixing and dilution systems support the semiconductor industry in achieving the high standards required for next-generation technologies. By ensuring precise gas delivery, we help semiconductor manufacturers maintain product quality, operational efficiency, and regulatory compliance in an ever-evolving technological landscape.