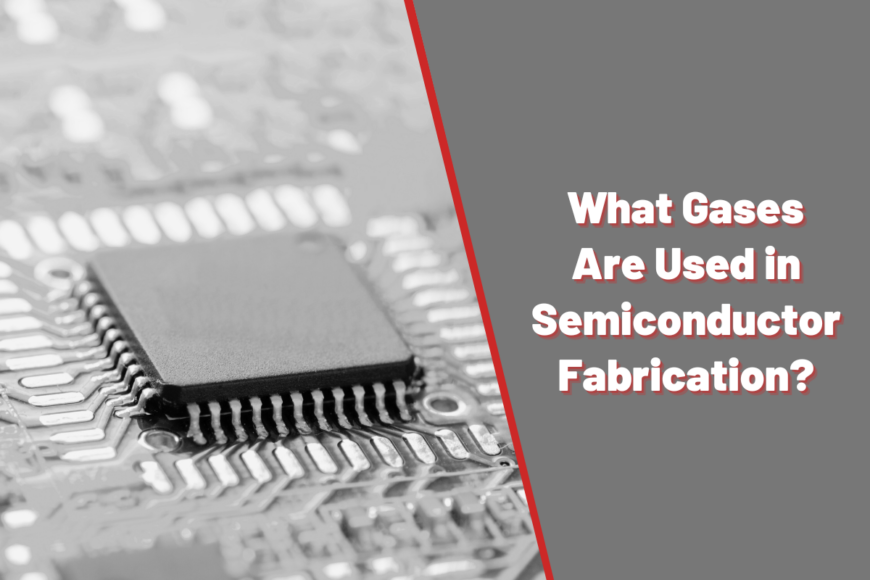
Semiconductor fabrication relies on a diverse range of specialty gases that play critical roles in processes such as deposition, etching, doping, and cleaning. These gases enable precise control over chemical reactions and material properties, ensuring the production of high-performance semiconductor devices. This article outlines the key gases used in semiconductor manufacturing, their specific functions, and how Environics supports gas management with advanced solutions tailored to the industry’s stringent demands.
Categories of Gases Used in Semiconductor Fabrication
Deposition, etching, dopant, inert/carrier, and cleaning gases are all essential categories in semiconductor manufacturing, each serving distinct roles in the fabrication process. Deposition gases are used to form thin, uniform material layers critical for electronic devices. Etching gases help create precise patterns on wafers by removing specific material layers. Dopant gases modify the electrical properties of semiconductors to achieve desired conductivity. Inert and carrier gases maintain stable processing environments, preventing unwanted reactions and supporting various process flows. Finally, cleaning gases ensure the purity and efficiency of manufacturing equipment by removing contaminants and residues.
The following table illustrates some of the types of gasses within each category, plus their primary purpose in semiconductor fabrication.
Category | Gas | Purpose |
Deposition Gases | Silane (SiH4) | Precursor for silicon-based films in CVD processes |
Deposition Gases | Germane (GeH4) | Depositing germanium layers for high-speed devices |
Deposition Gases | Ammonia (NH3) | Nitride film deposition for dielectric material and barrier |
Etching Gases | Chlorine (Cl2) | Reactive gas for anisotropic etching in plasma systems |
Etching Gases | Fluorine (F2) | Reactive gas for anisotropic etching in plasma systems |
Etching Gases | Sulfur hexafluoride (SF6) | Deep reactive ion etching (DRIE) for high-aspect-ratio structures |
Etching Gases | Carbon tetrafluoride (CF4) | Etching and chamber cleaning due to strong fluorine content |
Dopant Gases | Phosphine (PH3) | Source of phosphorus for n-type doping in silicon |
Dopant Gases | Arsine (AsH3) | Introduces arsenic as a dopant for transistors |
Dopant Gases | Boron trichloride (BCl3) | Facilitates p-type doping and contributes to etching |
Inert and Carrier Gases | Nitrogen (N2) | Carrier and purging gas to prevent unwanted reactions |
Inert and Carrier Gases | Argon (Ar) | Stable plasma environment for sputtering and ion implantation |
Inert and Carrier Gases | Helium (He) | Enhances heat dissipation and used for leak detection |
Cleaning Gases | Oxygen (O2) | Plasma cleaning to remove organic contaminants and residues |
Cleaning Gases | Hydrogen (H2) | Reduces metal oxides in reactive cleaning applications |
Cleaning Gases | Nitrogen trifluoride (NF3) | Effective cleaning gas for CVD chamber maintenance |
Functions of Gases in Semiconductor Processes
Thin film deposition relies on precise gas mixtures to enable the formation of high-quality films with controlled composition and uniformity, which are critical for device performance. The etching of microstructures involves reactive gases that selectively remove material, creating intricate patterns necessary for integrated circuits. Doping processes use specific gases to modify the electrical conductivity of semiconductor materials, a fundamental step in defining the functionality of electronic devices. Additionally, contamination control and cleaning are supported by inert and reactive gases that ensure fabrication environments remain free from impurities, thereby maintaining high product yields.
Purity Requirements
Maintaining Ultra-High Purity (UHP) standards is critical in semiconductor fabrication. Even trace levels of contaminants can cause defects, reducing device reliability and yield. UHP requirements are achieved through advanced purification systems that eliminate impurities from process gases, ensuring that only the highest quality gases are used throughout semiconductor manufacturing. This level of purification is complemented by rigorous monitoring practices, which involve continuous tracking of gas purity levels across the entire delivery system. These monitoring systems help detect any potential contamination in real-time, safeguarding the integrity of the fabrication process. Additionally, cleanroom protocols play an essential role in supporting contamination control. By maintaining strict environmental conditions and employing best practices in equipment handling and personnel procedures, cleanroom protocols minimize the risk of airborne and particulate contaminants affecting the production environment.
Involved in Semiconductor Fabrication?
Specialty gases are the lifeblood of semiconductor fabrication, supporting critical processes that define the performance and reliability of electronic devices. Environics’ precise gas handling solutions ensure the semiconductor industry meets its goals for efficiency, safety, and product quality.
We play a vital role in supporting the semiconductor industry with advanced gas management solutions. Our precision gas mixing and dilution systems enable accurate control of gas concentrations, which is critical for ensuring process stability and repeatability in semiconductor fabrication. These systems are designed to maintain consistent gas flow rates and compositions, reducing variability and enhancing product quality. In addition to standard solutions, Environics offers custom gas delivery systems tailored to meet the unique requirements of semiconductor fabs, whether for research and development environments or high-volume manufacturing operations. Our expertise extends to automated control and monitoring technologies, which enhance safety and operational efficiency by minimizing human error. These automated systems provide real-time data on gas flow, pressure, and purity, ensuring that semiconductor processes operate under optimal conditions at all times.
As technology advances, we continue to innovate, providing the gas management systems needed for the next generation of semiconductor manufacturing.