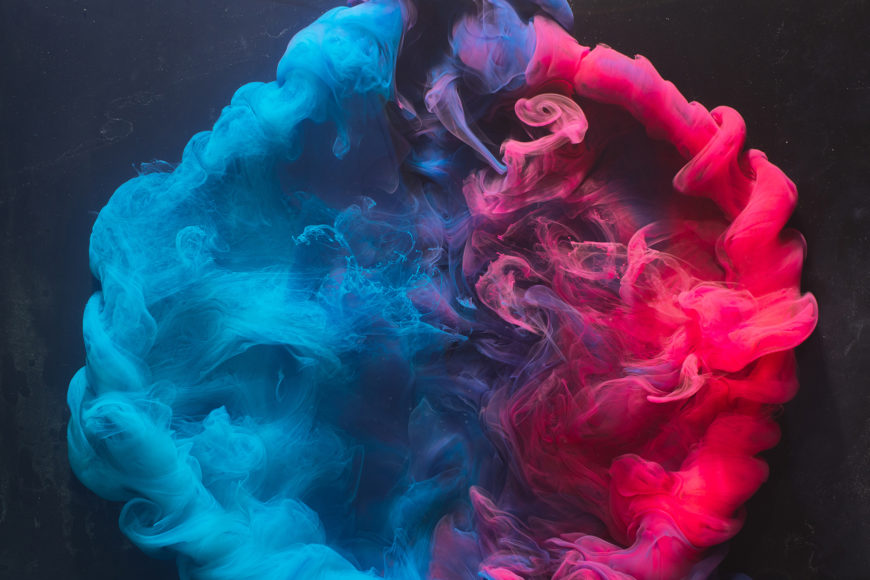
Gas blenders are essential for delivering precise and consistent gas mixtures in various applications. They have predominantly been used to produce pre-mixed gas blends for delivery and storage, but users are increasingly deploying gas mixers at-line and on-line for more efficient process control. Key applications include the calibration of analytical instrumentation, the generation of comparable gas streams for process control, for research in a wide variety of industries, and for a range of purposes in environmental monitoring. Given that precision is central to each of these applications, it’s essential that gas mixing systems prioritize accuracy. So, how does this work?
Gas blending systems typically employ a combination of mass flow control and gas mixing technologies to achieve desired mixing ratios, guaranteeing accuracy and reliability. At the core of a gas blender are multiple mass flow controllers (MFCs), which regulate the flow rates of individual gases. The actual working principle of a given gas blender depend on many factors, including the types of MFC used. Thermal MFCs, for instance, measure the flow rate of a gas stream passing through a sensor tube by applying heat to the gas stream and measuring the temperature differential as it exits the tube. This post will explore why this simple process is so effective in ensuring accuracy.
The Significance of MFCs in Gas Blenders
Thermal MFCs are vital for accurate gas blending systems, as they precisely regulate individual gas flow rates. Their performance and reliability are crucial for upholding desired gas mixture ratios. To appreciate their importance, it is necessary to explore the working principles and key features of thermal MFCs.
Working Principles
Thermal MFCs function based on the principle of heat transfer. As gas flows through the sensor tube of the MFC, it gathers heat when it enters the tube and transfers some heat back to the tube as it exits. The temperature differential in the tube is measured by two independent temperature sensors. The electrical signal generated by the sensors is amplified and transformed to a linearized signal that is commonly recognized by instrumentation. This process allows the MFC to maintain the desired mass flow rate.
If you’d like to learn more about the overarching principles of gas blending systems, refer to our article How do Gas Blenders Work?
Key Features
- Accuracy and repeatability: Precision in MFCs is vital for upholding desired gas mixture ratios. High-quality MFCs provide excellent accuracy and repeatability, ensuring consistency in the gas blending process.
- Wide flow rate range: MFCs cater to various applications and requirements by offering a range of flow rates. This flexibility allows gas blenders to accommodate different gas mixtures and concentrations.
- Fast response time: Swift response to flow rate changes is critical for maintaining accurate gas mixtures, especially in dynamic applications. Advanced MFCs deliver rapid response times, enabling quick adjustments and minimal overshoot or undershoot in flow rates.
- Multi-gas compatibility: MFCs can work with diverse gases, including corrosive or reactive gases, which is crucial for generating various gas mixtures. They can also be calibrated for multiple gases, offering flexibility to switch between different gas types without sacrificing accuracy.
Factors Affecting Gas Blender Accuracy
The accuracy of gas blenders is closely linked to the performance of the MFCs within the system. It is vital that these components are of high quality, well-calibrated, and maintained for optimal performance. Key factors contributing to gas blender accuracy include:
- Calibration and traceability: MFCs must be calibrated using reference gases traceable to national or international standards to ensure accurate and consistent flow rates.
- Gas mixing algorithms: Gas blenders employ sophisticated algorithms that calculate the correct ratios of individual gases to achieve the desired mixture, taking into account each gas’s unique properties, such as density, viscosity, and compressibility.
- Leak detection and prevention: Gas blenders use high-quality seals and fittings to prevent gas leaks from introducing inaccuracies in the blended gas mixture. All units must pass a stringent leak test during manufacturing.
Gas blender accuracy relies on various factors, including the quality of the MFCs, calibration and traceability, gas mixing algorithms, and prevention of gas leaks. By addressing these factors, gas blenders can maintain precise control over gas mixing processes, ensuring the reliability and accuracy required for critical applications across various industries. The combination of high-quality MFCs and diligent attention to these contributing factors allows gas blenders to consistently deliver accurate and reliable gas mixtures for a wide range of applications.